Verifying the Integrity of Composite Adhesive Joints using the ODiSI
Chicken rivets may not sound like a very technical term. However, it refers to the mechanical fasteners used extensively in the aerospace industry to guarantee the reliability of adhesive bonds of carbon fiber-reinforced plastic (CFRP) materials. Because adhesive bonds are not very well understood, current certification requirements need proof that should a critical design load be reached, each adhesively bonded joint will not separate and cause structural failure. The easiest and cheapest way to do this is to assemble the parts with these additional mechanical fasteners, or chicken rivets.
Do the additional fasteners compromise the part?
不幸的是,这些额外的紧固件实际上否定了粘合接头的许多主要益处,包括更高的关节刚度和优异的疲劳性能。而不是将负载均匀地转移到粘合界面,紧固件和孔中产生应力浓度。额外的紧固件加重,它们的孔通过水进入,湿度和腐蚀来鼓励环境退化。
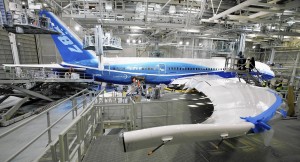
What can we do to better-understand the joint?
One way to accelerate the move away from chicken rivets is to develop a greater understanding of damage growth in bonded structures. Researchers have been using Luna’s distributed strain sensing system in order to assess the tough-to-detect flaws and damage that might affect the integrity of adhesive joints. How uniform is the load distribution? How does failure initiate and evolve? What model parameters should be used to analyze these joints?
Luna的odisi.platformallows for strain measurements to be captured at every millimeter along a continuous optical fiber sensor, allowing you to see the strain profile across the entire joint with a single scan. Any defects can be easily detected as steep strain gradients during both static and fatigue loading, and tracked accurately across the joint. In addition to that, the small fiber sensor size lends itself to being embedded directly into the bond line. This means that you now have a micro-local measurement at that joint. Finally, when a finite element model of the part is created, the ODiSI’s measurement points can be used to provide real-life calibration data across the entire structure. This is in contrast to being limited to the single points that you acquire using surface-mounted electrical foil gages.
What have other researchers learned?
The body of research is expansive and growing. Researchers from Mississippi State University showed that the addition of fiber sensors inside the joint does not at all impact bond strength (https://arc.aiaa.org/doi/abs/10.2514/6.2016-0239)。挪威的研究人员使用分布式传感器跟踪有意缺陷的生长,以准静态拉伸负载,并在整个去粘合过程中跟踪应变梯度(https://www.sciencedirect.com/science/article/pii/S1359836815000086)。In a multinational collaborative effort, Ribeiro and colleagues used the ODiSI system to evaluate the stability and rate of disbond growth (https://www.tandfonline.com/doi/abs/10.1080/00218464.2018.1433039.)。In these papers, accompanying finite element models were also created and used as cross-reference validation for the distributed strain measurements.
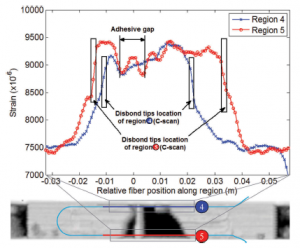
Conclusion
胶粘剂的使用关节越来越受人关注just in the aerospace industry, but also in the automotive and energy industries, for lightweighting and strength optimization. As such, it would be massively beneficial to be able to evaluate the integrity of these joints in a more robust and direct way.
要了解有关如何更好地了解粘合件零件的行为的更多信息,请查看我们的odisi.分布式传感平台。
参考资料
1 Fabricio N.Ribeiro,Marcias Martinez&Calvin Rans(2018)模式II疲劳脱粘采用中央切割层标本和分布式应变传感技术,粘连,土井杂志:10.1080/00218464.2018.1433039